Ryan Lusk, CEO from Branch Technology, discusses the status of 3D printing under construction.
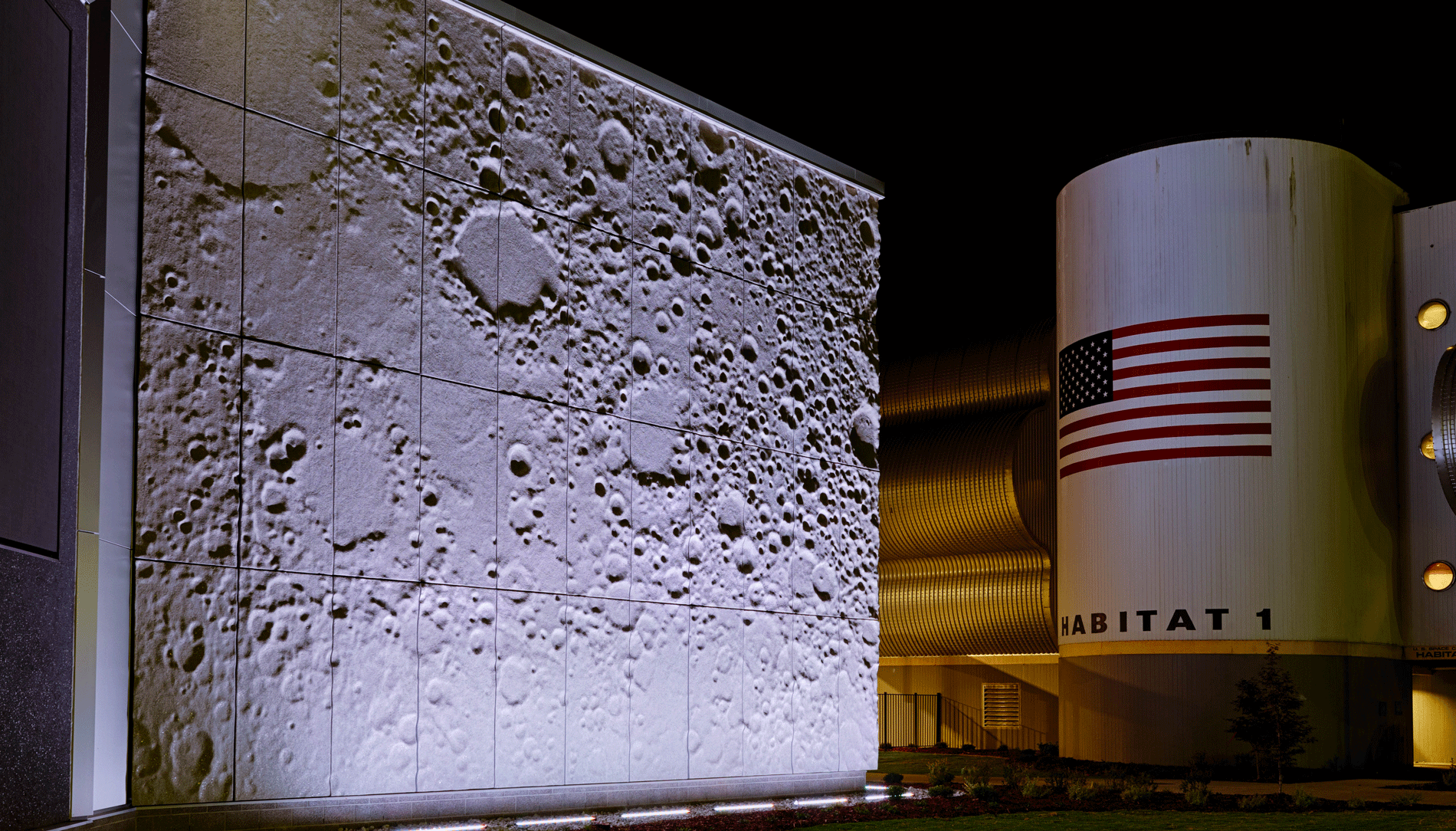
“If it is not broken, don't repair it,” should hang it over the door of every self -esteem technology. Unfortunately, the preferences for the updated version tend for many technology companies: “If it is not broken, there are not enough functions.”
Of course, it is not an easy thing to judge whether a product or a process is not broke. The pace of cultural, ecological and technological change in the 21st Century is that products and processes can become Just broke by staying static.
For example, take construction. It is a sector that is known for the fact that the old “if it is not broke”, and yet the pressure is increasing to find new, more efficient methods, since the demand for additional living space and revived infrastructure continues to increase.
What does it take to shake the construction from the lull?
How did it get there?
I sat down with Ryan Lusk, CEO of Branch Technology, to talk about where the construction sector leads and how the 3D printing fits this future.
Engineering.com: Why didn't you see that much technological disorders in construction compared to other sectors? Is it a question of having to overcome regulatory hurdles, or does it only depend on inertia?
Lusk: This is certainly the million dollar question. A few years ago there is a McKinsey study in which industries were classified by the introduction of new technologies and innovations. The construction was second to the end – only over the fish of fish.
Why is that? On the whole, there is an inertia component, but the construction is also a collection of sub -industries with competing interests and incentives. You have the design page with architects that use the latest software from early CAD and CAM to the present day of AI-controlled generative draft tools. This technology dramatically exceeded the manufacturing skills and cost effectiveness, which was a limited factor.
Then there is a development that includes cost structures and financing and finally the actual construction – the general contractors and installation teams. These groups often have competing incentives. Architects are usually not too aggressive to use new technologies. We jokingly say that you want silver medals – you don't want to be the guinea pigs.
Developers tend to be more open to technology, and on the side of the integrated world, general entrepreneurs already have to deal with a lack of experienced workers. They focus on what you already know, so it is a challenge to take on something new.
If you have evaluated these stakeholders through their priorities – design, costs, installation -, you will receive very different rankings, which creates a difficult environment for disorders. Everyone is profitable enough that they do not feel the need to be innovative or to use new technologies.
But in 50 or 100 years in the future, people could find it crazy that we all brought out these materials in the forest or in an open field, and then an army of workers on site would gather a structure. We would not do that for any other product that we buy.
How does this apply what you do with industry technologies here?
We print 3D a grid structure, which is referred to as a branch matrix and resembles the cell walls in our body and offers the overall shape, function and design. We then fill it with a foam with conversion and avoid it robotically to its final geometry.
The result is an incredibly light but strong composite product that is finely coordinated for various building applications.
This process falls under the roof of additive production. While most additive manufacturing approaches focus on how much material has to be overlaid – e.g. B. FDM printing or concrete pressure for residential apartments -we ask: “How little material can we use while we achieve the necessary performance and structural properties?”
In the 2024 financial year, we recorded growth of 300%, which is mainly due to our facade product for the outer building cladding. We also have several other applications in development.
Facades are mainly used for the new building. However, we have also developed a patented, energy -efficient retrofit product called Branch Regererates, which is currently being installed at the Kirtland Air Force Base in Albuquerque, NM.
This product follows a similar stack of materials, but includes additional steps. We start with a high-resolution lidar scan of the existing building, typically a 50- or 60-year-old structure with curved or cracked walls and architectural features. With this scan we create a 3D model that drives our production processes. Then we fill the back of our facade panels to enable architectural functions before we install them to improve the energy efficiency of the building.
Do you see the retrofit set that you follow in Albuquerque and elsewhere to overcome some of the hurdles to innovations that we have discussed?
Yes, exactly. In this case we actually have a regulatory wind. The mandates of the energy efficiency disintegrate for 2025 and 2030, and sustainability is first class for many. In addition, there is a real cost driver – some studies estimate that 40% of energy consumption is lost through the facade and the envelope of a building. This makes energy efficiency upgrades a priority from both regulatory and cost perspective.
At the moment there are not many good or inexpensive options. The tearing and reconstruction of a structure is not realistic – it is disruptive, expensive and requires approval and permits again. Removing and replacing an existing facade is also severely disturbing and often requires the tenants to clear the building. The development of a quick, inexpensive hermit system makes a lot of sense. By producing components asynchronous, while other trades are working on their parts, we save enormous time and work on the construction site.
On the subject of work, it is known that the construction of a lack of work is confronted. Does your technology answer this challenge or is it more orthogon?
It depends on the project, but Labor is a big factor. In order to promote acceptance in the construction industry, you need the “holy grail” of cost parity or even savings. We often compete with prefabricated GFRC [Glass Fiber Reinforced Concrete] Panels and other heavy, bulky products.
That is why we carried out a case study on a 50-story tower, where we hope to work on it. The facade was originally prefabricated for prefabricated GFRC or architecture. Instead, the use of our facade panels would save over £ 34 million compared to these alternatives. This reduction enables the plate edge to be reduced from 15 inches to about 6 inches on all 50 floors.
From the point of view of the work, traditional FEARGA -FECAST time and specialists require and weld heavy panels. In contrast, our panels can be installed with a simple swing lift or a cherry picker.
Where do you see the construction work over the next 10 years? And how do you see 3D printing or branch specifically to play on it?
I think the adoption curve accelerates new technology. I just took part in the Retech Conference in New York. It was really exciting and encouraging to see the dynamics for all things, the Proptech and Contech: smart homes, smart buildings, data management and energy management technologies.
There is a distinction between residential and commercial applications in construction. Different technologies win in individual tractions. In residential areas, companies such as Icon do fascinating work with 3D printing. In the commercial, the approach will have a greater influence if we refine our products to influence more of the entire budget and the scope of the project.
An application that we look forward to are temporary homeless accommodation. Our technology enables us to create easy, quick -compiled accommodations that can be set up in an hour or two. They are safe, have lockable doors, self -leveling feet and HLK and offer a worthy housing solution. The leasing model makes these shelters an inexpensive solution for cities, municipalities and non -profit organizations. After use, they can be renovated and transferred to the needy to areas, be it for homeless warehouse, natural disaster aid or refugee apartments.
Another particularly funny and meaningful project that we carried out was the new Space Camp Operations Center of NASA, in which you will bring in the next generation of MINT students who hopefully will be the astronauts and engineers of tomorrow. After we had received something with them with them what the building should look like, including the facade and a large entrance, we were able to get a lidar scan of the actual surface of the moon. With this data we have recreated the surface of the moon on both sides of the building.
It is a really nice recovery in the actual surface of the moon, but it also serves as a symbol. In the early days we focused on extraterrestrial applications while we developed this technology. Now we bring it back to earth to solve problems here.